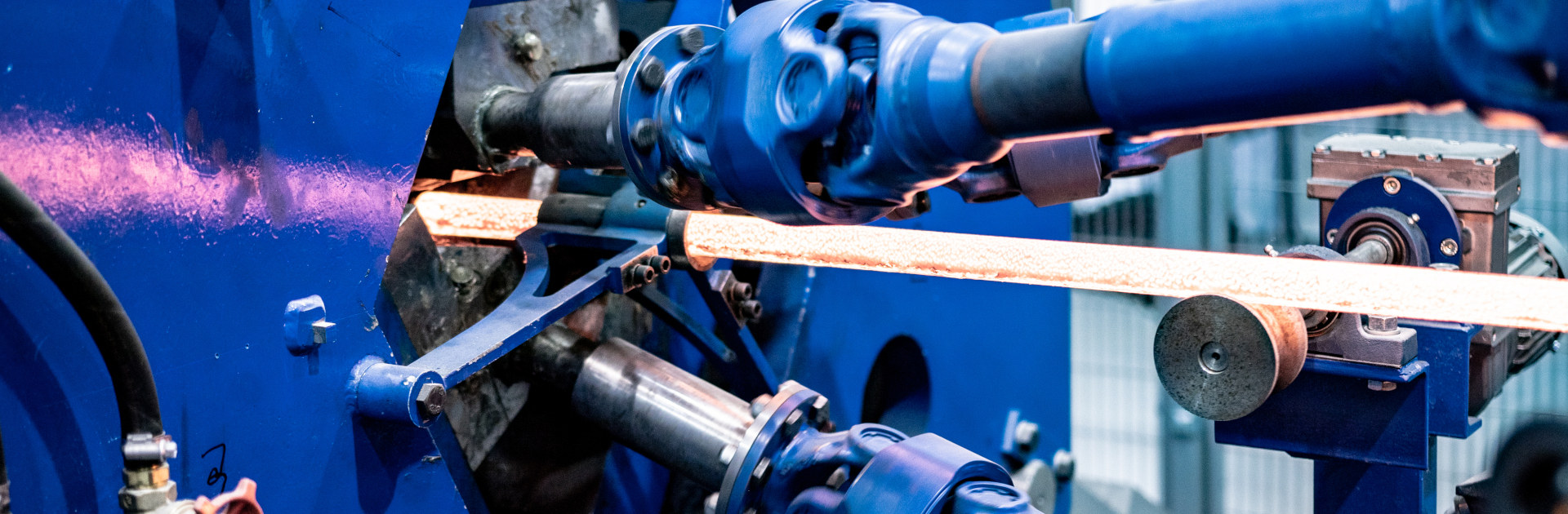
Experimental forming laboratory
The Experimental Forming Laboratory deals with conventional forming processes such as forging or rolling as well as special methods such as incremental skew rolling, semi-solid processing or press hardening. It also has a hardening room for heat and thermomechanical processing of various types of materials, including parts after 3D printing. Using material-technological modelling it is possible to test and optimise real forming and heat treatment processes. This can lead to improved efficiency and reduced energy consumption of a process, or to better mechanical properties of a final product. A new feature is the development of materials for hydrogen storage (powder materials and high-entropy alloys). The laboratory also has its own specimen production facilities, including for the production of very small test bodies using electrical discharge machining and waterjet cutting.
DESIGNING AND OPTIMIZING REAL FORMING AND HEAT TREATMENT PROCESSES
Material-Technology Modelling (MTM) is used for designing and optimizing real forming and heat treatment processes.MTM can determine the influence of the parameters of the production process on the existing technology and on the properties of the final product with its subsequent optimization. MTM can be used not only to adjust processing parameters but also to make material substitutions. These procedures are complemented by FEM calculations in DEFORM or by calculation of material properties in JMatPro software. Input data is obtained by measuring real processing processes with a thermal camera, pyrometers, thermocouples or a high-speed camera for dynamic forming processes.
HEAT TREATMENT AFTER 3D PRINTING
Additive manufacturing technologies for producing a wide range of parts are coming to the fore. 3D printing introduces large internal stresses to the material due to repeated heating during the sintering of the individual powder layers. After the printed parts are cut off from the platform or even during printing, the deformation, cracks or other internal defects may occur. This can be prevented both by selecting the appropriate printing parameters and by using a suitably designed subsequent heat treatment. This also creates the desired mechanical properties of the printed parts. The Laboratory of experimental forming focuses mainly on the heat treatment of metal 3D printed components from materials such as maraging and stainless steels and nickel alloys.
HEAT AND THERMOMECHANICAL PROCESSING OF STEELS AND ALLOYS
One of the main interests of the laboratory is the development of new processes and technologies for the heat and thermomechanical processing of modern high-strength steels (from first to third generation). These are mostly multiphase steels that use a number of strengthening mechanisms to achieve the required mechanical properties. Unique mechanical properties are achieved by the new processing routes. Due to the presence of residual austenite in their structures, these steels also exhibit excellent strain hardening in cold deformation. The laboratory is also involved in research and development of materials for the energy industry, focused on optimizing the heat treatment of steels currently used in the energy sector.
DEVELOPMENT OF NEW ALLOYING CONCEPTS AND FORMING PROCESSES FOR TOOL STEELS
The department is also involved in the research of the process of forming high-alloy tool steels and the design of modifications of their chemical composition. The combined processes of forming and heat treatment produces structures with uniformly dispersed carbides of alloying elements. It is also possible to design new chemical compositions of steels that will achieve the required properties for specific purposes. The materials prepared in this way are used to produce inserts with better properties than those using conventional processing.
LABORATORY EQUIPMENT
Tools for press hardening
Shaped parts made of high-strength steels are currently produced by press hardening (PH). These are mostly components for car bodies, but also other structural parts, e.g. in transport and handling technology. PH steels which have been specially developed for this technology are highly suited to these applications, as well as high-strength TRIP steels or Q-P steels. PH steels are developed directly for processing in press hardening tools without the need for further heat treatment. The laboratory currently has two press hardening tools for different sizes of input sheet metal. Both tools can be heated to process multiphase steels with special heat treatment profiles. The latest tool variant is split and allows material tailoring during processing in the tool. Other concepts include, for example, the integration of a Q&P process or intercritical annealing into the machining process.
Thermomechanical simulator
This is a testing machine equipped with a high-frequency resistance heating system with a heating rate of up to 200 °C.s-1 and a sophisticated cooling system that allows a wide range of heating or thermomechanical processing experiments to be carried out easily and accurately. By precisely controlling the temperature, strain and forming force, test specimens can be subject to various heating and thermomechanical processing profiles. The machine has a load force of up to 50 kN, a strain rate of up to 2000 mm.s-1 and a maximum heating temperature of 1500 °C. These parameters mean it is possible to precisely follow the prescribed processing parameters and to perform physical simulations of real technological processes such as free forging, wire rolling, incremental forming, press hardening and thermal or mechanical loading of parts in industrial applications. Furthermore, mechanical properties can be determined at high temperatures and high strain rates. Input data for FEM simulations can also be measured on this device.
Equipment for development of incremental forming
The HDQT-R 30-12 is a rolling mill designed for reducing the diameter of round bar stock by scew rolling. The individual modules (induction heating, cooling nozzles, water bath, tempering furnace), enable variants of thermo-mechanical processing of bar steel to be tested. The equipment allows the creation of cylindrical, conical and other predefined rotationally symmetrical shapes with a straight longitudinal axis. A wide range of steel grades can be processed, from carbon steel to stainless structural steel, as well as special steels such as titanium or nickel alloys.
DHI-10 series induction heater
In addition to standard furnace equipment (electric atmospheric furnace, chamber furnace with protective atmosphere), the workplace also has manual induction heating. The different shapes of the induction coils allow local heating of different types of semi-finished products from sheet metal to bulk parts. By local heating before or after heat treatment or forming, the mechanical properties can be modified, for example, by tempering the hardened structure in the area requiring higher ductility. Centralised heating can be carried out to impose local deformation or for forge welding of heterogeneous joints. The heating rate can be controlled by the induction power. Due to the rate of heating, there is no significant surface hardening and the size of the coil makes it possible to precisely define the processing point. It is also possible to process shaped blanks.
Other equipment
Water jet cutter
MEBW-60/2 electron beam welder
Equipment for bending and folding precise sheet metal blanks
FASTCAM SA-X2 high-speed camera
Electrical discharge machine (EDM)
DHI-10 series induction heater
A range of furnaces for heat treatment
Chamber furnace with inert atmosphere
Thermal camera